Step-By-Step Guide To Component Sense's Inspection Process
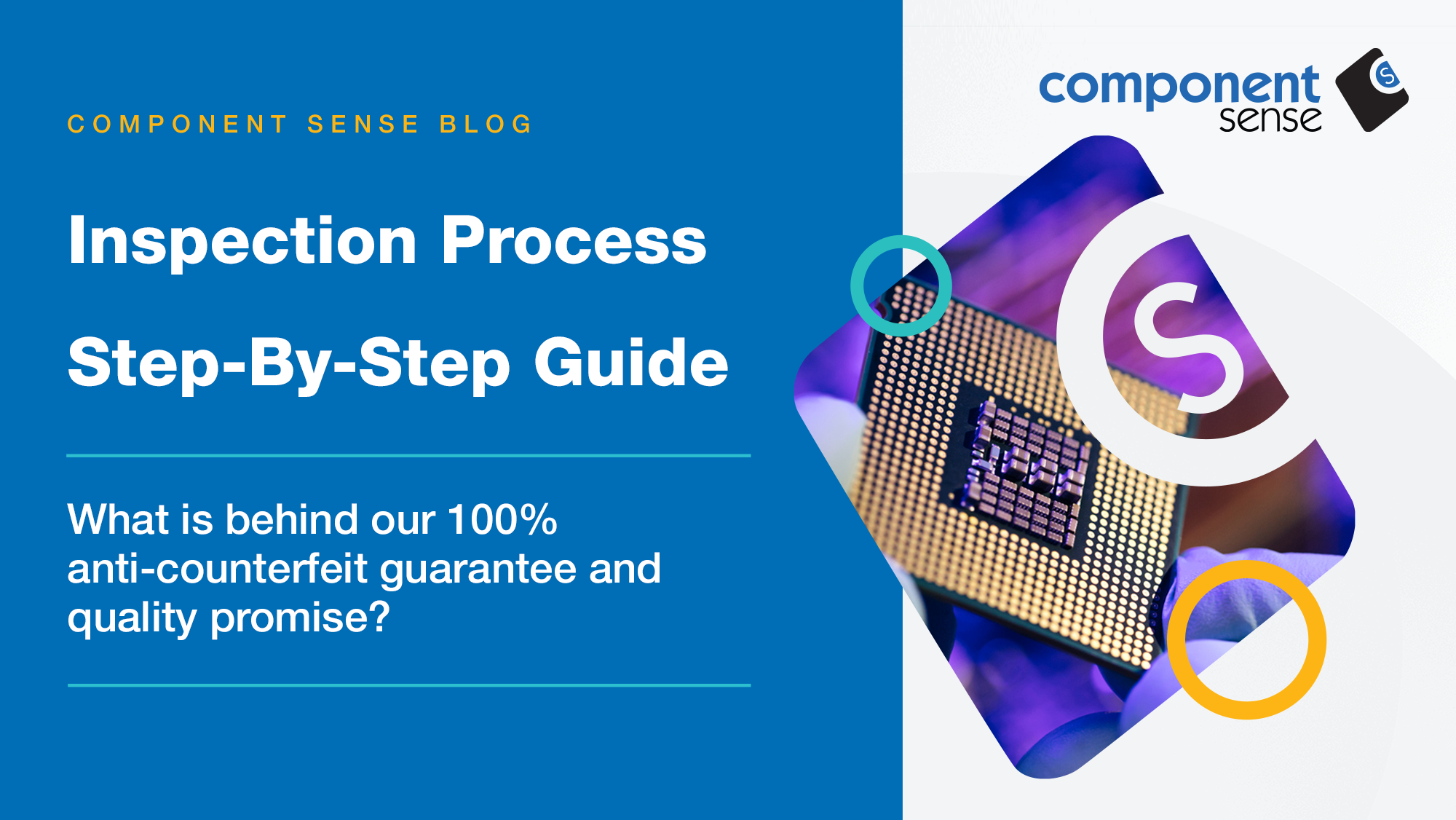
Two of major reasons buyers choose Component Sense is because of are our unique 100% anti-counterfeit guarantee and promise of quality.
Yes, we only source products from large OEM (original equipment manufacturer) and EMS (electronic manufacturing service) companies that already have high levels of safety built into their supply chains. But this traceability only scratches the surface of why buyers choose Component Sense with confidence.
Setting the foundation for trust in Component Sense is our state-of-the-art inspection process. Our warehouse staff are expertly trained in counterfeit detection using our bespoke system and the latest in cutting-edge equipment. Counterfeiters are crafty, so we always stay one step ahead.
Component Sense’s inspection process will vary depending on the component type, for example, whether the chip has balls or leads. In saying that, the process usually takes at least 40 minutes. This guide will just focus on the key details you need to know.
“The inspection process as a whole, every step of it, is important. We do not know where these components end up. Some of the parts we inspect and send out could end up in healthcare or aviation, and lives could depend on it,” said Warehouse Inspector, Norbert Szucs.
1. Carry out pre-inspection checks
Before starting, it is essential to note that our warehouse is an ESD (electrostatic discharge) controlled area. That means no food or liquids are allowed, the space is kept at the perfect temperature (20 - 21 degrees Celsius) to not damage the delicate silicone or other metals, and other ESD prevention procedures must be followed. Inspectors also wear gloves to prevent unintentional damage from fingerprints and natural oils.
We carry out pre-inspection checks before we look at the components in question. To do this, our inspector logs into our custom-built warehouse software system to pull up details of the order that has been quoted to our buyer. At this point, we will reserve the components to ensure they are secured during our lengthy process.
Our warehouse system will then direct the inspector to the quoted stock within our secured storage. Looking at the datasheet and our records, we will cross-reference data, including:
- Type of commodity, for example, switches or resistors
- Whether the components are RoHS certified (Restriction of Hazardous Substances and Electronic Equipment)
- msl levels (moisture sensitivity level)
- General legitimacy of components
It is essential to know the commodity type, as it determines whether the order must adhere to tariffs set by certain countries. The msl level is also vital information to look for as it informs us whether parts are moisture-sensitive and need to be handled accordingly. As standard, msl-level components will be vacuum-sealed in dry packaging to prevent damage from moisture in the air.
2. Count the parts
The fine piece of machinery you can see in this image is our Versacount reel counter. As the name suggests, this device counts the number of components on a reel. That way, we can accurately check that the number of parts (sometimes in the thousands) matches what our warehouse system and its packaging label show. Our inspector also ensures the reel runs clockwise per the industry standard.
If components do not come in a reel or tray and are loose in a bag, they will be tallied using a precise counting scale. Although unlikely, we will also inspect for any damage to reel tape due to vacuum sealing. If we encounter any deviations whatsoever during this step, the components will already head straight to NCR (non-conformance reporting).
3. Check existing inspections
When we first receive brand-new, unused components (which everything we redistribute is), we also conduct a robust inspection before parts go into secure storage. That way, we can dig into our custom warehouse computer software to look for any previous images or notes on file when parts are quoted.
We would still reinvestigate even if notes were looked into and debunked during the previous inspection.
“The combined knowledge and experience of our team spans over 100 years. We are trained to the highest standards,” explains Warehouse Team Leader, Steven Waterson.
4. Inspect the outer packing
You can tell a lot about the quality of components by the packaging they come in, especially when it comes to catching counterfeits. Each type of box or packaging will have a slightly different inspection process with specific abnormalities we look for. It is a big red flag if the box does not meet manufacturer standards or is not in pristine condition.
Another giant red flag for counterfeit components is the state of the label on the packaging. At this step in the process, our expert inspector will meticulously scan the label for many issues, including:
- Incorrect spelling
- Professional formatting
- The expected font
- Manufacturer’s seal (unless it has been officially repacked, which we will query)
- Whether the bar codes and alphanumeric labels match up with what is provided by the original manufacturer
Finally, the barcode on the packing will be scanned to see whether the information checks out. If the barcode is damaged, this potentially indicates a big problem.
5. Examine the inner packing
Step five: we are not even halfway through the inspection process and have not put any components under the microscope. As well as being packed in a box, most reels and trays of components will be secured in either an ESD bag or a vacuum-sealed msl bag.
Like the exterior box and labelling, we will closely cross-reference the inner packaging and its label for consistency. The condition of internal packaging will also be examined to see if the data matches what we have on file.
“We have an extensive, extremely detailed inspection process that includes over 100 check points to ensure our customers receive authentic devices,” said Steven.
6. Survey the carrier
Now, our Component Sense inspector moves on to surveying the carrier. A carrier protects the components during storage and transport, whether in a reel — like in the above image — or a tray. In most cases, the carrier will also have a distinguishing label like the interior and exterior packaging.
An issue we have encountered in the past is the country of origin not matching up with what is on other packaging. It is also a red flag if the msl level indicates the components require vacuum-sealing and the parts are not packed in that way.
When inspecting the carrier tape or tray, we pay close attention to its condition and for any signs of tampering, like an unexpected matte finish or high sheen. Another sign of counterfeiting is when the orientation of the chips does not match what we have on file or the datasheet.
The images below highlight incorrect orientation and wrong tray size vs what we hope to expect from the original manufacturer. When components are uneven, it usually indicates that they are not in the original tray. This could be because the original manufacturer ran out of trays, or it could be due to something more sinister. Regardless, we would need to investigate further.
7. Visually inspect the component
We are not pulling out the heavy-duty microscope just yet! Before we do that, our Component Sense inspector needs to use his keen eye to inspect the tape, tray or tube. At this stage, we are paying close attention to the tape to look for obvious inconsistencies like the condition of the tape and that all of the pin one locations (the small dimple on the component) are the same. The images below show varying sizes of the pin one marker in the same reel.
We cut a delicate incision in the tape using a special scalpel (just like a surgeon) to remove one of the microchips. If a particular component catches our eye, we will remove that. The experience of our warehouse team means there is never any damage done by doing this.
While cutting the component out of the tape, we are looking for any sign of contamination pointing to the parts being counterfeit, tampered with or corroded. Some small details we look for include:
- Solder on the lead ends showing they have been used in the past
- Dust indicating parts did not come from the typical cleanroom manufacturing plant
- Corrosion showing improper care and handling
- Consistent texture on the components in the tape
8. Examine the top of the component under a microscope
Now, it is time to bring out the big guns. By that, we mean our Keyence microscope. Component Sense has several microscopes at our disposal, but our Keyence, in particular, is our most powerful device. Specifications of the Keyence microscope include:
- High-resolution imagery up to 6000x
- Depth of field for the complete picture
- 3D rendering to ensure precise measurements of components match with the datasheet and other examples we have on file
Now that the component is finally under the microscope, we can see the fine details and potential defects not obvious to the naked eye. There is a long list of abnormalities that indicates the part has been tampered with or is counterfeit.
In the very crude example images below, you can see evidence of remarking in the form of paint lines (shadow marking). In this instance, we can use an acetone wipe to reveal what is hiding below. Our Keyence microscope allows polarised photos (anti-glare) to catch further, much more subtle inconsistencies.
After analysing the text on top of the chip at 50x magnification, we pay close attention to the texture of the surface and the overall quality of the leads or balls at 220x magnification. Obvious issues to watch out for include scratches or chips pointing to prior use, and the number of leads or balls match the datasheet and information in the system.
In terms of the overall texture, we expect to see peaks and troughs that are evenly distributed, not an overly smooth finish that may indicate remarking. While zoomed in to this degree, it is also an excellent chance to check out the pin one marker. This small circle must look like an authentic laser etch or dimple. Many counterfeiters struggle to replicate this.
9. Examine the bottom of the component under a microscope
At this stage, we flip the component over and carry out similar inspections to those we did on the top side. At this point, a significant variable is whether the texture on the bottom of the component is consistent with the top (unless the datasheet indicates that a textural difference is intended).
While under the microscope, we ensure that the logo, country of origin, bottom pin one locator, number of leads, and any other defining features match what is on the topside and original manufacturer's datasheet. If the manufacturing date on the top and bottom of the chip does not match, this issue requires further investigation.
We also look for signs of previous handling, scratches, debris and damage.
10. Inspect the component’s leads under a microscope
The smallest but arguably most important part of our quality inspection comes in the form of leads or balls. For this blog, we will use the example of leads. Any slight damage or deviation to the leads can harm the component's performance. Given the leads are made from copper, the reflection of light can be a challenge. We use optimal side lighting and our Keyence microscope to highlight textures in detail to mitigate this.
Once we have a clear picture of the leads, we look for other defects, including:
- Abnormal texture
- Discolouration
- Corrosion (example below)
- Stress fractures
- Contamination
- Oxidisation
As well as the condition of the top side of the leads, keen attention is also required for the bottom of the lead feet (Pads). This is where the chip is soldered onto the circuit board. There may be solderability concerns if there are any signs of discolouration, major exposed copper or corrosion as in the below image.
When inspecting BGA (ball grid array) components, we will review the balls under a microscope for any signs of damage caused by residue from re-balling, corrosion, test marks or flattening. If there are variations in height, this can cause a void, meaning not all of the balls come into contact with the circuit board.
In the example below, you can see scratches that may have been caused by previous use.
11. Examine the sides of the component under a microscope
Next up in our inspection process is taking a good look at the sides of our component sample. We do not mean to sound like a broken record, but many of the abnormalities and texture consistencies we looked for on the top and bottom of the component will also be inspected on the sides.
Top coating is one of the unique traits of counterfeit that is easiest to spot from the side profile. As seen in the example below, top coating is a visible line indicating a new layer has been added to one or both sides of the component to cover up the original markings.
12. Cross-reference the country of origin
As mentioned in a prior step, cross-referencing the country of origin is a key tool in determining whether a component is counterfeit. So much so that we have a dedicated step in our inspection process to look for any inaccuracies.
13. Present the outcome
Last but certainly not least, Component Sense inspectors like Stevie compile the full inspection report and pass on any findings to our customers. If there have not already been clear problems noted in the inspection process so far, a final decision will now be made as to whether the components are fit for redistribution.
Given Component Sense’s 100% anti-counterfeit guarantee and quality promise, even slight questions or concerns lead to failure. If the components we inspect fail, they are moved to our quarantine bay pending further investigation, and we will inform the customer.
“Quality is the keystone of how the department operates. From the beginning of the order fulfilment process until the packages are dispatched for delivery, we take great pride in the services we provide,” explains Steven.
Confidently purchase electronic components with Component Sense
As you can see, a lot goes into Component Sense’s inspection process to ensure nothing slips through the cracks. This guide is only the tip of the iceberg for our team's analysis. If there are still concerns after our internal inspection, we would then escalate the components further for XRF (X-way fluorescence) examination and decapping.
At Component Sense, we are proud of our promise of quality and 100% anti-counterfeit guarantee. If you have any further questions about our extensive inspection process, contact the Component Sense warehouse team: sales@componentsense.com
You can view our range of brand-new, never-used traceable components online.