Rare Earth Elements And Electronic Components: Your Questions Answered
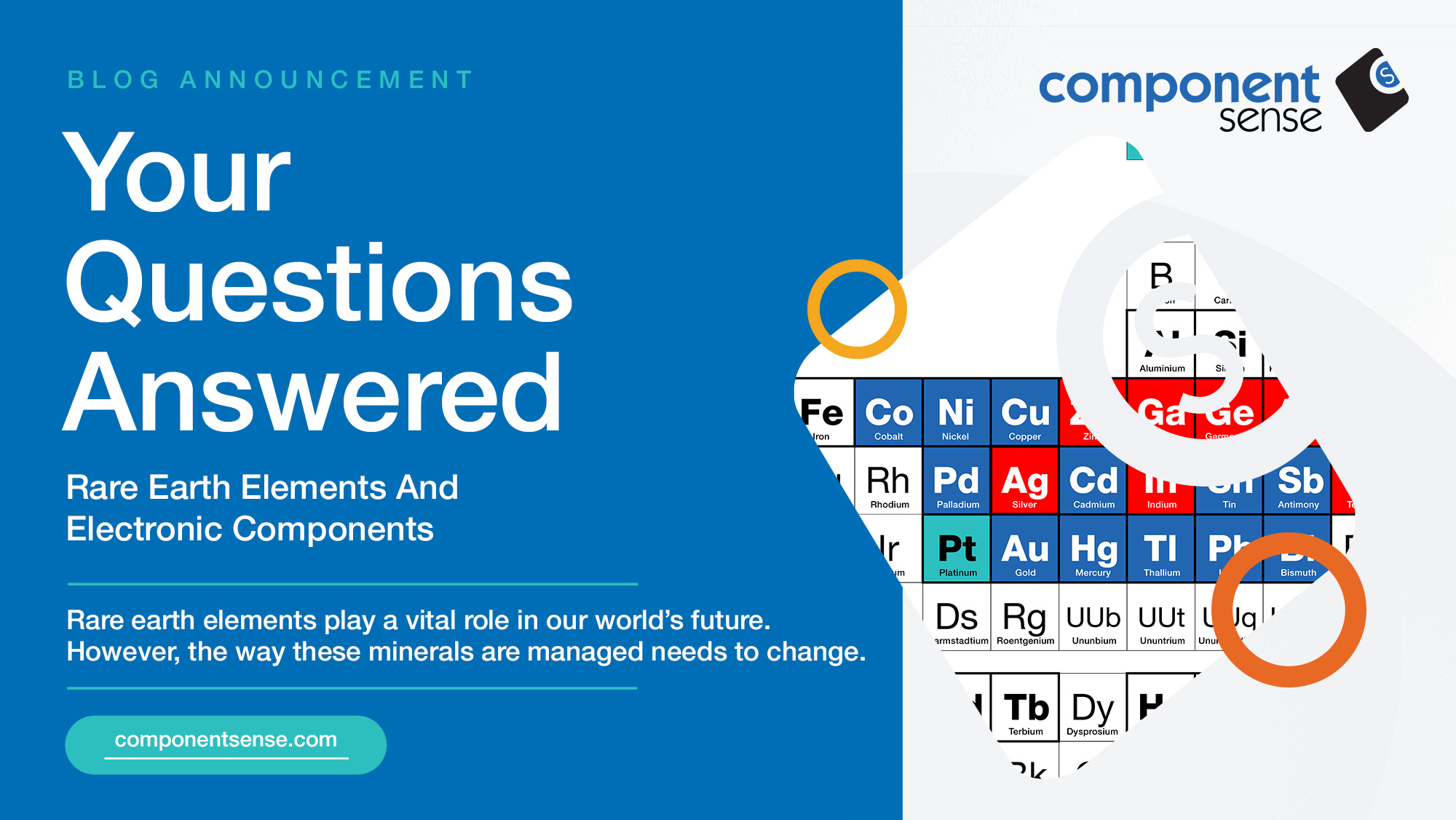
When the average consumer picks up their smartphone and scrolls social media, they do not consider what goes into their device.
Why would they? If they did, perhaps more of a spotlight would be put on controversies surrounding electronic waste (e-waste) and the rare earth elements used for the components of their devices.
The term rare earth metals or elements (REEs) is misleading. In reality, there is an abundance of these REEs spread throughout the earth’s crust. The challenge is that REEs are not found in high concentrations, and their geothermal properties make it difficult for miners to separate pure metal from deposits.
Geopolitical tensions and environmental concerns have generated robust discussions around REEs in recent years (causing expensive headaches for electronic manufacturers, in turn). Resolving concerns is crucial, given the growing importance of these minerals for green technologies and life-saving equipment. Studies predict the global demand for REEs could reach 51.9 thousand metric tonnes by 2030. This blog will answer some of your burning questions on the topic.
What are the rare earth elements?
Seventeen rare earth elements can be found in the middle of the periodic table. These REEs fall into one of two categories based on their atomic numbers:
- Light (More common): Gadolinium, samarium, promethium, europium, neodyium, lanthanum, praseodymium and cerium.
- Heavy (Rarer): Ytterbium, thulium, lutetium, terbium, holmium, erbium and dysprosium.
Yttrium and scandium have atomic numbers of 39 and 21, so they are not considered light or heavy. Yttrium and scandium are still grouped as REEs, given they have similar chemical properties and how they are found as ores.
Top tip: The atomic number of an element refers to the amount of protons present in the nucleus of each of its atoms. An element’s number of protons makes it unique and determines its properties.
What is the role of earth elements in electronics?
Many of these REEs are used in electronics and microprocessors for their unique electrochemical, luminescent, or magnetic properties. Another distinguishing feature is that REEs can be both used in their pure form and alongside other elements.
Common examples of REEs in electronics include:
- Scandium for high-performance alloys for batteries
- Terbium for phosphors in television displays
- Neodymium for magnets in many components
Neodymium is the most common REE used in microprocessors, given its strong magnetic properties, energy efficiency, and high thermal stability (some chips can get quite hot while in use). Neodymium is an essential element as components get smaller and smaller.
There are often 40 critical raw materials (not all REEs) in a smartphone alone. Given this number, you can see why there are even concerns about running out of certain minerals over the next 100 years.
What are the ethics of rare mineral procurement?
The difficulty in attaining many metals needed for electronic components, coupled with the increasing demand, has led to numerous controversies. These challenges trickle down the supply chain to disrupt electronic manufacturers and eventually hit consumers in the pocket.
Unlike fossil fuels, where the eventual goal is to stop reliance altogether, REEs are considered crucial to society's sustainable future. The conversation is not about whether we should continue utilising these rare minerals or not, but instead, how to use them in a more sustainable manner.
Geopolitical tensions
75% of rare earth mineral reserves are on Russian, Vietnamese, American, Brazilian and Chinese soil. However, China makes up 85% of global REE production, followed by Australia with about 10%. The U.S. was the largest producer of REEs in the 1960s, but those days are long in the past.
The relationship between China and the U.S. has been turbulent — to say the least — in recent years. In 2010, China imposed taxes and quotas on their REE supply, stating concerns about the environment and domestic resources. This move sent shockwaves through the global community, with countries stockpiling and investing heavily in seeking new sources of these crucial minerals.
Understandably, these rare metals have been a prominent topic in the geopolitical rivalry between China and the U.S. President Joe Biden passed the Inflation Reduction Act in 2022, which aims to promote the production of critical minerals for use in clean energy. This also helps to reduce the countries’ reliance on China and Russia. The global market size of rare earth metals was valued at $13.2 billion in 2019, and it is expected to grow to $19.8 billion by 2026.
Labour issues
There are varying mining methods, depending on where you are in the world and what you are mining for. Regarding rare earth mineral mining, the work is usually dirty and treacherous.
The dangers of mining for REEs are particularly prominent in certain African regions. There are few labour protections, low pay, and little to no health and safety protections. In some politically unstable areas, armed groups use forced labour to mine and sell REEs to buy weapons. This trend led the EU to ban conflict minerals from being exported to the EU.
Harm to the environment
At Component Sense, we are passionate about championing environmental change and understanding how our environment affects the electronics supply chain. At the end of the day, our business actually aims to lessen the need to mine by creating a circular economy. We are well aware of the environmental impact of mining, from habitat destruction to pollution. However, mining REEs is a necessary evil, as these rare earth minerals are required for many life-saving and green technologies.
Many REEs are located in carbonates or peralkaline igneous rock systems. In most cases, miners must leach the ground with acidic chemicals to get the sought-after REEs. Runoff and other contamination from this process can harm local habitats and water sources.
Less than 1% of REEs are recycled. Extracting tiny amounts of minerals from vast volumes of discarded electronics is challenging. Not all hope is lost, however. The EU’s Horizon 2020 programme invested $16 million in SUSMAGPRO (Sustainable Recovery, Reprocessing and Reuse of Rare Earth Magnets). As the name suggests, SUSMAGPRO aims to use magnets to extract and then reuse precious metals.
How can a business be more resilient to potential future REE shortages?
Tackling issues around the procurement of REEs can not be brushed under the rug, given the importance of these minerals for a more sustainable future. However, it may seem like a catch-22, as mining rare earth elements is contentious. It is difficult to predict the future of these minerals and their accessibility to electronic manufacturers. However, there are ways you can better prepare for whatever the future holds. Ultimately, circulatory is the aim of the game.
Carry out a Life Cycle Assessment
As with many business processes, taking a step back for a holistic view of your operations can be helpful. The same can be said for evaluating the environmental impact of the electronics you manufacture.
When carrying out a Life Cycle Assessment (LCA), consider the extraction of REEs and how they are disposed of or recycled at the end of your product's lifecycle. That way, you can identify design improvements, end-of-life management strategies (recycling), and other measures to ensure your products have less environmental impact. Taking responsibility is key.
An LCA can be broken down into three steps:
- Inventory analysis: Compile data on energy and material use
- Impact assessment: Examine environmental impacts of energy and material use
- Interpretation: Conclude and make recommendations
Redistribute your excess and obsolete components
When China limited REE supplies in 2010, other countries explored new mining areas and recycling programs. One way your business can be more circular and prevent e-waste is to redistribute your excess and obsolete (E&O) component stock.
The global electronics industry produced 59.4 million metric tons of electronic waste (e-waste) in 2022. Nearly all of this will include valuable rare earth minerals. By redistributing your excess inventory, you are keeping REEs out of landfills and reducing reliance on controversial mining practices.
OEMs often sit on an average of 10% of their revenue in E&O stock. Redistributing your excess with Component Sense can return up to 100% of its value, making financial and environmental sense.
Responsible sourcing
Electronic manufacturers are consumers as well. As such, businesses need to be picky with where they source materials, including rare earth metals. When you can, work with suppliers that adhere to responsible mining practices like the Cobalt Initiative and try not to overforecast. While you may think it is a good idea to stockpile components at a lower unit price, it can be counter-productive in the long run.
Traceability is a vital part of our quality assurance at Component Sense. By fully tracing the lineage of all the components we redistribute, we can proudly offer a 100% counterfeit-free guarantee and quality. The ethos of traceability should also carry over to what electronic manufacturers demand from REE miners.
Futureproof your supply chain with Component Sense
It is widely accepted that rare earth elements play a vital role in our world’s future as we create more green technologies to tackle climate change, advance quantum computing, and increase AI-related technologies. However, the way REEs are managed needs to change.
Component Sense is proud to promote a circular electronics industry. We implore you to learn more about the topic and look for ways you can integrate sustainability into your supply chain, including when it comes to reliance on rare earth minerals. Read more about how Component Sense is championing change for inspiration for your business.