Quality Assurance: Confidence Through Traceability and Teamwork
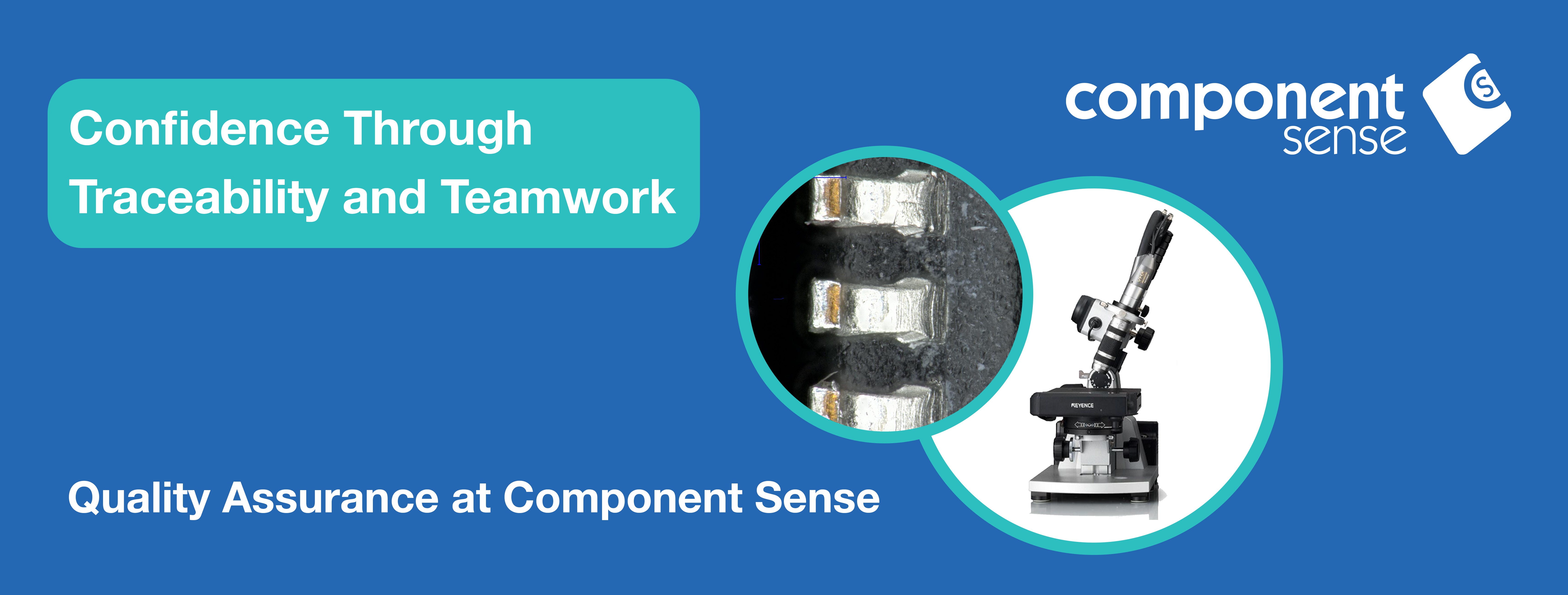
At Component Sense, we aim to provide all our customers with top-of-the-range electronic components which are 100% counterfeit-free, traceable, and reliable.
Our fundamental aim is to ensure that our customers feel satisfied and confident and that their needs are fulfilled. So, how does the Component Sense team achieve all of this?
Component Sense focuses on its EPIC values both to create a positive workplace and ensure customer satisfaction. At Component Sense, ‘quality assurance’ encompasses the manual and systematic efforts we undertake in order to protect our customers’ needs and expectations when it comes to electronic components. Ultimately, Component Sense put an extensive amount of effort into making sure our customers are happy.
Kenny McGee, our founder/CEO, says that “Component Sense was created in response to my time spent at one of the major franchised electronic component distributors. The service being provided was well below the standards I expected and however hard I tried, it was impossible to make a significant impact on the service levels of the company. When I set up Component Sense in 2001, customer service was my number one priority. Our dedication to customers continues to this day.”
Traceability
Within Component Sense, traceability refers to our capacity to fully trace the lineage of our electronic components. Thanks to our strict policy of only purchasing electronic parts directly from tier-one OEMs and EMSs, we can accurately track components from manufacturer to market. This primary purpose of traceability provides a record of the item's history, which is then used to minimise risk and comply with regulations. Component Sense’s Quality Assurance Department can thus understand a component's origin in full and conduct their inspection processes with as much knowledge as possible.
So, why is traceability so important within the electronic industry?
“Counterfeit components started to hit the market in 2005,” says Kenny McGee. “To ensure that we would never be negatively affected by counterfeit products, we began a relentless pursuit of the best anti-counterfeit inspection in the industry. We worked with some of Scotland's best universities to come up with the ultimate anti-counterfeit inspection process. However hard we worked, we discovered that at some point, a human had to decide whether or not a part was compliant. Despite the massive advances in technology since then, we still see reports from our competitors that are vague and inconclusive. We inspect to a very high standard using the best equipment available. However, we realised that the only way we could fully guarantee authenticity was to sell factory traceable stock. We began this process in 2007 and have not bought from untraceable sources since.”
At Component Sense, we combine top equipment and staff training to ensure that all our electronic components are fully traceable and 100% counterfeit-free. Our updated inspection process started in 2009 and continues to allow the company to sell traceable stock, thereby consolidating our position as a trusted source. In an industry where counterfeit products and corner-cutting are unfortunately common, Component Sense’s thorough inspection process gives peace of mind to customers. We are proud to stand out with the confidence that our components meet high standards and comply with all regulatory requirements.
Component Sense’s Inspection Process
Our extensive inspection process requires time, focus, and a meticulous eye for detail. Of central importance to the Component Sense team is accuracy. By paying as close attention as possible to all aspects of the components that come into our warehouse, we can efficiently work towards our ultimate goal of customer satisfaction.
The detailed procedure involves 15 key checks, with 129 questions included. Here are some of the notable steps within the quality assurance process:
- Count
- Check existing inspections
- Package type
- Outer package inspection
- Inner package inspection
- Carrier visual inspection
- Component visual inspection
- Microscopic top inspection
- Microscopic bottom inspection
- Microscopic leads inspection
- Microscopic side inspection
- Return samples
- Country of origin
- Outcome
- Complete
After a member of the Quality Assurance Department has inspected and analysed the component, the next stage is finalising the packing of the item. Whilst our packing stage is less extensive than that of inspection, it still takes time and attention to detail.
The stages involved in the packing process are:
- Gather stock
- Note Location
- Take photograph
- Box
- Take evidence
- Print labels
- Display item value
- Finalise with Component Sense branding
Ultimately, our Quality Assurance Department can therefore monitor that all stock that enters and leaves the warehouse is of a consistently high standard that will both meet company requirements and elevate the customer’s experience. “The quality assurance process is very important for the team as it is one of the main goals of the company,” says Warehouse Manager, Steven Waterson, “amazing service starts in the warehouse with our quality checks.”
Teamwork
The second most important element of Component Sense’s quality assurance process is its people. When hiring, we recruit for values over skills. As a company, Component Sense is passionate about its EPIC values. To be EPIC, we are Enterprising, Positive, and we work with Integrity and Clarity. “By hiring people that are already EPIC and share our values,” says Kenny, “we can maintain the high levels of customer service that the company was founded on. Care and attention to detail are key. Our focus has always been on retaining customers for the long haul and making them raving fans.” Being EPIC is a continuous process: we have regular team-building events, we emphasise lifelong learning and development, and we hold monthly communal book clubs to focus on our team culture.
Component Sense’s central aim is to make customers feel valued and know they can trust our products and performance. Thanks to our fantastic Quality Assurance Department, a commitment to quality is standard practice within the business. As well as this, all necessary quality control processes have been refined, so we are confident that electronic components delivered to our consumers are flawless. This combination of EPIC values, traceability, and teamwork has resulted in long-term customer loyalty and retention!
We are always looking for EPIC people to join our growing team, and Component Sense is currently hiring for several positions. If you are interested, you can find us on LinkedIn or Indeed.
If you are looking for 100% traceable, reliable, and counterfeit-free electronic components, you can be confident in the quality of Component Sense. All our parts are new, unused, in stock, and available immediately. We hope this article has shown you the importance of quality and customer service at Component Sense.
We welcome any feedback or any request for price quotes via sales@componentsense.com. Thank you!
LinkedIn | Instagram | Twitter | Facebook