Keeping REEs in a Circular Supply Chain
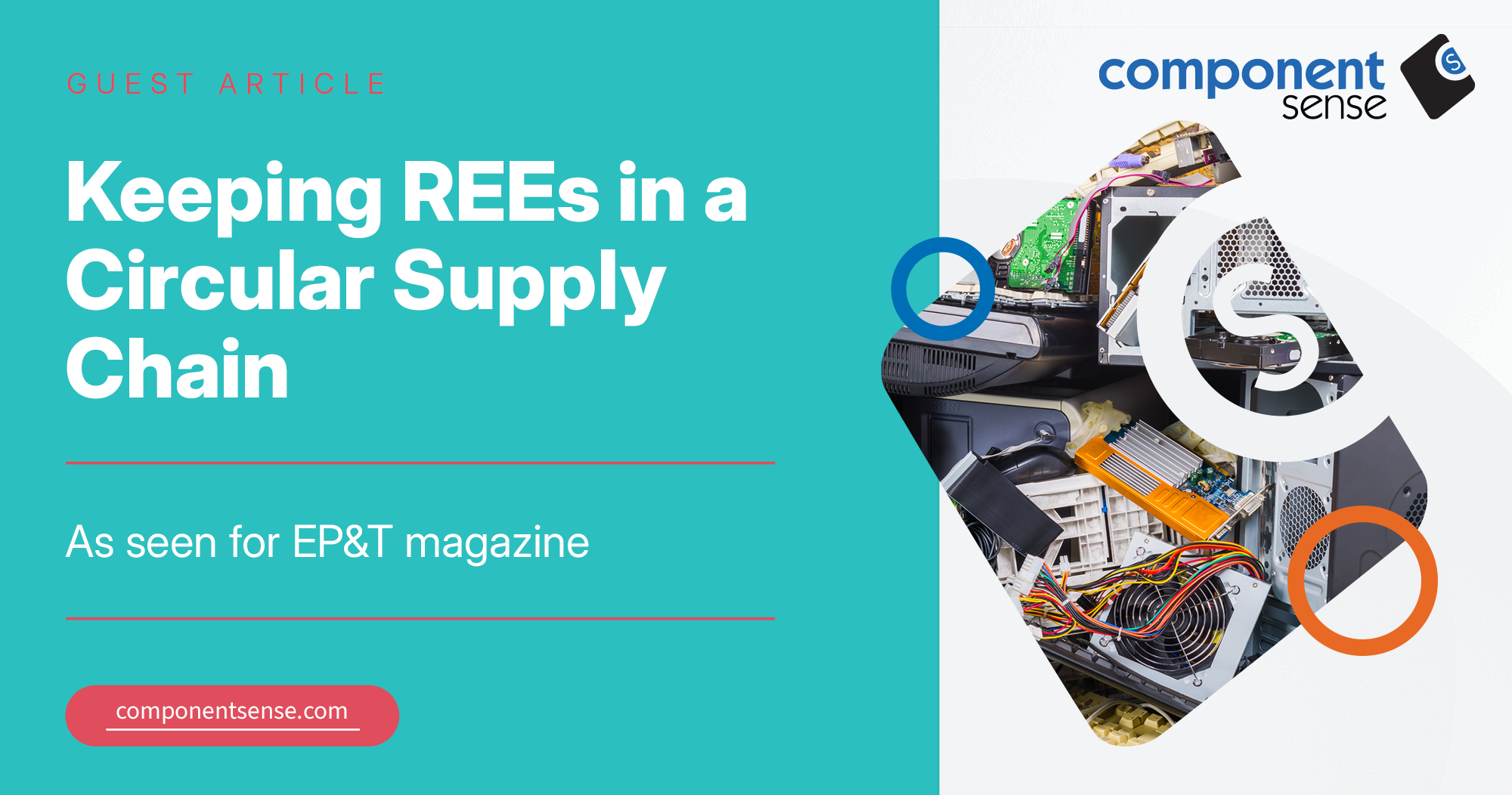
This guest article written by Component Sense was originally published by EP&T magazine in November 2024.
The International Energy Agency predicts that the demand for rare earth elements (REE) could increase three to seven times what it is now by 2040 [1]. Unlike fossil fuels — a finite resource society is gradually moving away from — REEs are crucial to our sustainable future.
Rare earth elements (REEs) include 17 metallic elements. These metals are essential in electronics for their electrochemical, luminescent, and magnetic properties. Lanthanum, cerium, and neodymium are indispensable for devices from semiconductors to batteries.
Truth be told, REEs are not that rare. In fact, their small concentrations and challenging extraction are primarily what makes them highly sought after. Recent geopolitical tensions and environmental challenges, especially between the U.S. and China, have sparked discussions about new resource extraction and the global supply chain.
Although recycling e-waste is better than landfill disposal, there are more effective ways for the electronics industry to reduce pollution and minimise excess mining. Prioritising a circular supply chain is an actionable solution for managing REEs more sustainably.
Current REE mining practices
As of 2023, China accounted for over two-thirds of the world’s rare earth mine output, with the U.S., Australia, and Russia also hosting significant mining operations [2].
Several common methods are used for mining REEs, with open-pit mines often set up to extract large quantities of ore. From there, the ore is smashed and crushed. The next stage typically involves gravity or magnetic separation, flotation, or chemical leaching with acids or alkalis to isolate the REEs.
Although several standard mining practices exist for REEs, each presents significant sustainability challenges. For each ton of REE produced, 1 ton of radioactive residue, 13 kg of dust, 75 cubic meters of wastewater, and 9,600–12,000 cubic meters of waste gas are estimated to be generated [3].
The harmful effects of REE extraction also go beyond environmental damage. In certain regions, REE mining is linked to poor labour conditions. In response, the EU introduced the Conflict Minerals Regulation [4].
Circularity in electronics explained
Today, only about 1% of REEs in discarded products are typically recycled, mainly due to logistical challenges and associated costs [5]. Recovery usually requires strong mineral acids and hydrometallurgy.
The order of the three Rs—reduce, reuse, and recycle—is intentional. Reduction and reuse should always be prioritised before recycling. A circular economy keeps products and materials like REEs in use for as long as possible while at their highest value. Recovery or recycling should then come as a last resort.
In the electronics sector, key principles of circularity involve manufacturing products and modifying operations to minimise waste. Circularity may also include regenerating natural resources.
Strategies for circularity
With the key pillars of a circular supply chain in mind, electronic manufacturers can adopt several strategies to improve their business operations. By doing so, they can also inspire industry peers to follow suit.
Circularity pushes companies beyond recycling REEs to reimagining product designs and adopting new sourcing methods. While regulations like the EU’s Critical Raw Materials Act aim to drive change, manufacturers must take proactive steps and lead the push for circularity.
Actively manage inventory levels
Excess and obsolete (E&O) component inventory may account for up to 10% of an electronic manufacturer's annual revenue. Many companies' stock sits idle in warehouses due to over-forecasting or unexpected market changes. Ultimately, this component stock is often written off, becoming e-waste that is either scrapped or sent to landfills.
To keep electronic components and their valuable REEs in a circular supply chain, companies should consider redistributing their E&O stock on the secondary market. Partnering with a business like Component Sense can make this process seamless.
Surplus inventory that is brand-new, unused, and fully traceable to the original manufacturer can be valuable to other companies. If redistribution is approached correctly, it prevents e-waste while recuperating costs, leading to a 100% return on cost prices in some cases.
The right-to-repair
Whether planned obsolescence is intentional or simply a side effect of the pace of technological advancements, the right-to-repair movement is growing just as fast. Consumers and governments increasingly demand that electronic devices be repairable easily and independently.
Ultimately, extending a product’s life cycle is key to keeping electronics and REEs in a circular economy. Consumers increasingly recognise the right-to-repair movement’s impact and support forward-thinking companies like Fairphone. The Fairphone 4 features eight repairable modules, along with spare parts, repair guides, and a robust take-back and refurbishment programme [6].
Extended Producer Responsibility (EPR) initiatives are holding more manufacturers accountable for their products through end-of-life. The Waste Electrical and Electronic Equipment (WEEE) Directive is driving change in the EU, while Canada is implementing similar EPR initiatives for electronics, packaging, and batteries.
Sustainable sourcing
The global nature of REEs results in complex supply chains that make tracing mineral origins challenging. Geopolitical tensions further discourage data sharing. However, procurement professionals must verify the sourcing of materials in their components if possible.
The good news is that tracking the origins of materials in supply chains is becoming increasingly straightforward. The EU is mandating Digital Product Passports (DPPs) to promote circularity, particularly in the electronics sector [7]. DPPs create a digital twin for physical products, simplifying access to important sustainability data.
A prime example is Volvo’s battery passport for its EX90 models [8]. This passport ensures Volvo complies with the EU’s upcoming battery passport requirements. It allows consumers to trace the origins of raw materials and assess the battery’s carbon footprint [9].
Procurement professionals should explore the secondary market as a sustainable source for components. With proper due diligence, the secondary market offers brand-new, unused excess and obsolete components that would otherwise end up in landfills. Secondary market sourcing keeps REEs in a circular supply chain and reduces the need for further extraction.
Compare recycling options
Less than a quarter of the world’s 62 billion kg of e-waste was recycled in 2022 [10]. This is partly due to the challenges of recycling common electronics, like slim smartphones with hard-to-remove batteries. To make matters worse, REEs are especially difficult to recycle from e-waste due to their low concentrations in devices.
A truly circular supply chain keeps REEs in use for as long as possible. Once all other options are exhausted, manufacturers should carefully compare recycling methods to select the most sustainable approach.
Arguably, there are currently no perfect e-waste recycling solutions available. Pyrometallurgy (smelting) often consumes large amounts of energy to heat e-waste and emits significant pollution. Hydrometallurgy relies on aqueous chemistry and leaching agents to extract REEs but produces hazardous waste. Bioleaching, which uses microorganisms to leach REEs, is a promising approach. However, it is considered slow and less scalable.
Conclusion
The REE market is projected to expand further due to rising electric vehicle production and the growth of the renewable energy sector. As demand rises, electronic manufacturers must support circular practices to keep REEs in use and reduce the need for new extraction. At the end of the day, REEs are a finite resource. The secondary market offers an effective solution to promote circularity by allowing unused surplus parts to be repurposed instead of becoming e-waste.
Circularity is crucial to sustainability. By choosing to prioritise a circular economy, electronic manufacturers have the opportunity to drive real, positive change.
References
[1] https://www.technologyreview.com/2024/01/05/1084791/rare-earth-materials-clean-energy/
[3] https://hir.harvard.edu/not-so-green-technology-the-complicated-legacy-of-rare-earth-mining/
[4] https://policy.trade.ec.europa.eu/development-and-sustainability/conflict-minerals-regulation_en
[5] https://www.sciencedirect.com/science/article/abs/pii/S0048969723074405
[7] https://blog.worldfavor.com/the-eus-new-digital-product-passport-dpp-everything-you-need-to-know
[11] https://www.royalmint.com/aboutus/press-centre/turning-electronic-waste-into-gold/
Come say hi to us on social media!